Introduction
The new EDT Series Thread Mill Series is designed to machine precision threads in a range of materials including hardened steels up to 66HRC. Our thread mills deliver improved cutting and chip removal, reducing the risk of the cutting tool breaking off inside of the hole.
Additionally, one thread mill can perform a variety of applications including right-hand thread milling, left-hand thread milling, and fine threading simply by changing the NC program. Cutting load is much smaller than conventional taps, and special toolholders are not needed.
Additionally, one thread mill can perform a variety of applications including right-hand thread milling, left-hand thread milling, and fine threading simply by changing the NC program. Cutting load is much smaller than conventional taps, and special toolholders are not needed.
Features
1.Features of Epoch Thread Mill
- Tough and strong edge design for threading in hardened steels.
- Tip shape reduces cutting resistance and suppresses tool bending.
- Drastically reduces tool breakage
- PN Coating provides excellent adhesion and wear resistance
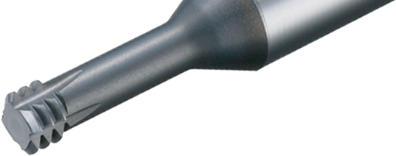
2.Features of Epoch D Thread Mill
- No pilot hole needed. This single tool can perform both drilling and threading simultaneously.
- High-strength edge shape design suppresses edge tip breakage in severe machining environments including hardened steels.
- ATH Coating delivers improved hardness and oxidation resistance.
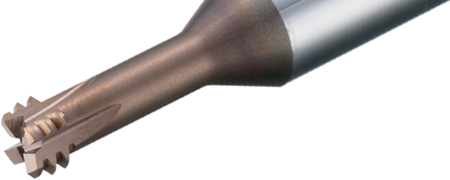
3.New PVD Coating Technology
Advanced TH (ATH) Coating: With a hardness of 3800Hv and oxidation temperature of 1200°, our new ATH Coating enables longer life and higher efficiency when cutting high-hardness materials (55HRC or higher). Compared with our previous generation coating, double the tool life and more than double the machining efficiency can be achieved. The ATH Coating is ideal for both dry cutting and wet cutting in a variety of materials including cold-worked die steel, HSS, tool steel, composite materials, carbide alloys and more.
PN Coating: By optimizing the AI content, the multi-layer PN Coating exhibits both excellent heat-resistance and adhesion to the tool substrate. Combining of the AlCr coating layer with Si produces high hardness (3000HV) as well as good wear resistance. PN Coating provides extended cutting tool life in both wet and dry machining of materials including pre-hardened steel, carbon steel, alloy steel, stainless steel, H13, D2 and more.
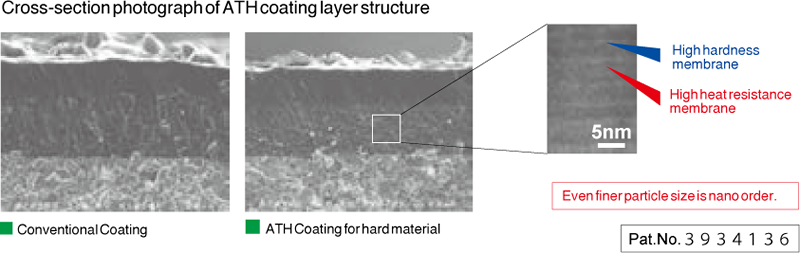
PN Coating: By optimizing the AI content, the multi-layer PN Coating exhibits both excellent heat-resistance and adhesion to the tool substrate. Combining of the AlCr coating layer with Si produces high hardness (3000HV) as well as good wear resistance. PN Coating provides extended cutting tool life in both wet and dry machining of materials including pre-hardened steel, carbon steel, alloy steel, stainless steel, H13, D2 and more.
4.Technology
Reduces the risk of tool breaking
By using a tool with a diameter smaller than the inside diameter of the thread, cutting chips are smaller and chip evacuation is improved. The risk of the tool breaking off inside the hole is reduced as a result.
One tool – various types of thread milling Right-hand, left-hand and fine thread milling can be performed by just changing the NC program. The nominal diameters of the coarse threads and fine threads that can be processed with the same tool are different. (Example: For ET-1.25-16-PN, coarse thread is M8 × P1.25 and fine thread is M10 × P1.25).
Cutting conditions can be freely set Unlike when using taps, synchronizing the rotation and feed rates is not necessary. Thread mills can be used in the same manner as end mills and cutting conditions can be set according to the processing environment.
Usable on a variety of machines Thread mills can be used even on machines with lower-powered spindles. In addition, special tooling such as tapping holders are not necessary.
Provides good finished surfaces Interrupted cutting suppresses gouging to provide good finished surfaces.
Thread milling can be performed to the bottom of the hole Epoch Thread Mills are designed with no incomplete crests and Epoch D Thread Mills have only one incomplete crest, making them ideal for when you want to perform thread milling to the bottom of shallow holes.
One tool – various types of thread milling Right-hand, left-hand and fine thread milling can be performed by just changing the NC program. The nominal diameters of the coarse threads and fine threads that can be processed with the same tool are different. (Example: For ET-1.25-16-PN, coarse thread is M8 × P1.25 and fine thread is M10 × P1.25).
Cutting conditions can be freely set Unlike when using taps, synchronizing the rotation and feed rates is not necessary. Thread mills can be used in the same manner as end mills and cutting conditions can be set according to the processing environment.
Usable on a variety of machines Thread mills can be used even on machines with lower-powered spindles. In addition, special tooling such as tapping holders are not necessary.
Provides good finished surfaces Interrupted cutting suppresses gouging to provide good finished surfaces.
Thread milling can be performed to the bottom of the hole Epoch Thread Mills are designed with no incomplete crests and Epoch D Thread Mills have only one incomplete crest, making them ideal for when you want to perform thread milling to the bottom of shallow holes.
5.Machining Process with Epoch Thread Mill
Catalog Download
PDF files are in Adobe's Portable Document Format. To view them you need Adobe® Reader® by Adobe Systems Incorporated.